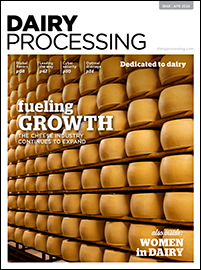
Fresh ideas. Served daily. Subscribe to Dairy Processing's free newsletters to stay up to date about the latest dairy news. |
Subscribe |
A leading dairy product supplier, known for producing high-quality cheese, sought to modernize its packaging operations. As a result, the company looked to an automated solution that could enhance efficiency, maintain product consistency, and reduce waste for its customers in the cheese block packaging process.
The company had been using a manual packaging process involving molding and stamping methods, requiring extensive labor and causing variability in product. The discrepancy in the shape of the cheese block created an increased risk of waste due to imperfect packaging.
The inconsistency was compounded by the fact that cheese is a living product affected by factors such as pH, temperature, and moisture levels. These variables can impact its firmness, shape, and overall stability, making packaging a challenge. If cheese blocks are exposed to temperature fluctuations or remain on the line for too long, they can begin to sag or lose their structural integrity, resulting in increased waste and processing delays.
As demand grew and automation became a priority, the company sought a solution that would standardize operations across multiple facilities and improve overall throughput. As a result, it implemented Massman Automation’s 40-Pound Cheese Block Case Packer, a specialized system designed to streamline packaging for large cheese blocks. It offers a fully automated process to enhance efficiency while minimizing product waste.
Massman’s Case Packers handle all aspects of the packaging process. They first pick case blanks and stage the boxes to accept cheese blocks. As the cheese blocks enter the machines, they are loaded into wrap-around corrugated collars before being pushed and sealed into the case blanks. At exit, an optional integrated palletizer receives the packages and stacks them onto a pallet in a configuration specified by the customer. For instance, palletizers are often programmed to stack cheese blocks in a pattern that allows air to flow between the boxes to aid in the cooling process.
Unlike other case packers that handle cheese, the Massman solution applies high pressure while pushing cheese blocks into the cases. This feature helps to pack the cheese more tightly and achieve a more consistently square shaped product.
Increased efficiency was achieved as the automated system is capable of processing approximately 24 to 25 cheese blocks per minute, a rate that exceeds most others in the industry. It is also significantly faster than cheese producers that still package cheese blocks by hand at a rate of only about three blocks per minute.
Furthermore, product quality improved through consistent block squaring, which reduces deformation and is critical for downstream automation at customer facilities. Since the cutting machines don’t adapt well to variability in product sizes, the intentional squaring of the cheese allows more slices to be cut from each block with less of it being sent to the shred line.
The dairy company’s packaging engineer highlighted the importance of automation in maintaining consistency and repeatability to meet customer demands. “With cheese, every variable—temperature, pH, and handling—affects the final product. The Massman case packers provide the reliability and adjustability needed to ensure we deliver a consistent, high-quality product to our customers.
Additionally, maintenance of the case packer has been manageable because of the system’s simple, reliable mechanical design, allowing in-house teams to perform troubleshooting and adjustments with ease. The Massman Automation Case Packer has been proven to provide years of trouble-free operation if maintained properly, as evidenced by the dairy company’s original machine still in service after many years of use.
Darin Kicker, sales engineer for Massman, testifies to the durability of the case packers. “Our machines are built with extremely high quality,” he said. “They are made to last, and if you keep up the maintenance on them, they will virtually last forever.”
Ongoing support has played a key role in the success of the case packer. Massman Automation representatives have been involved throughout the lifetime of the machines, assisting with equipment modifications, onboarding new equipment operators, and providing service.
The packaging engineer added, “I worked with Bernie Bryce at Massman a lot when I first onboarded. He walked me through the theory of operations about how the case packers worked and helped develop an adjustment guide for optimizing equipment performance.”
By implementing Massman Automation’s 40-Pound Cheese Block Case Packer, the dairy company has successfully transformed its packaging process, improving efficiency, reducing waste, and enhancing product quality. The investment in automation has not only streamlined internal operations, but also reinforced its reputation as a leader in the dairy products industry by ensuring that its customers receive a reliable and consistent product.
Fresh ideas. Served daily. Subscribe to Dairy Processing's free newsletters to stay up to date about the latest dairy news. |
Subscribe |