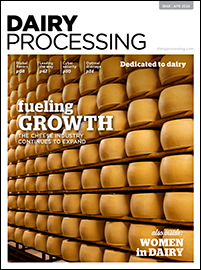
Fresh ideas. Served daily. Subscribe to Dairy Processing's free newsletters to stay up to date about the latest dairy news. |
Subscribe |
The drum motor is a one-component conveyor belt drive used for powering belt conveyors in a variety of industries, including airline baggage conveyors, food processing, postal parcel, aggregate, mining, and others. The drum motor is a unique belt drive as there are no external rotating parts.
The input power cable passes through the hollow shaft and is connected to the motor stator. The electric motor is mechanically connected in-line to the gear reducer. The drum motor is partially filled with oil. The oil inside the drum motor lubricates all mechanical components and helps to dissipate heat generated by the electric motor and gear reducer onto the drum, and from the drum to the belt. In theory, the drum motor is cooled by the belt making full contact with the rotating steel drum.
With the motor and gear reducer in-line, the drum motor eliminates mechanical losses, as is the case with traditional external motor and gearbox systems. The only mechanical losses are in the gear reducer itself, which is 2% per stage of reduction. The majority of gear reducers in VDG Drum Motors are two-stage, with some having three-stages depending on the desired belt speed. As a result, the mechanical losses of the drum motor may range between 4% and 6%, making it the most efficient belt drive on the market today.
However, as compared to traditional external motor and gearbox drives, the drum motor, which offers efficiency, safety, and space savings, has not been all that popular with the belt conveyor industry. The new generation of drum motors designed and manufactured by VDG aims to change this.
The electric motor
An important feature of a standard electric motor is an external cooling fan. Without a cooling fan, the temperature of the electric motor will keep increasing to the point of distraction.
In order for an electric motor to produce rotation, a rotating electromagnetic field is needed. To achieve that, it requires ferrous and nonferrous materials, such as iron and copper or iron and aluminum. The stationary part of an electric motor (the stator) has motor windings that are copper and a laminated stator core that is iron. The rotating part (the rotor) of the electric motor is made up of iron laminations and aluminum bars.
When an electric motor is running, the magnetic density produces the rotating electromagnetic field from the stator core and the rotor generates heat that needs to be dissipated. The other heat source of an electric motor is the heat generated by the copper motor windings as electricity passes through them and draws electrical current (measured in amps) to produce the rotating magnetic field.
In summary, an electric motor has two heat sources. The heat generated by the electric motor windings due to current density, as well as the heat generated by the stator core and rotor core due to magnetic density. The electric motor will fail if it cannot dissipate the heat generated by the current density and magnetic density.
When looking at the drum motor, one can see that there is no cooling fan. So, how do you dissipate heat from the electric motor and gear reducer in the drum motor? Originally, it was thought that the oil would transfer heat from the motor and gear reducer to the drum, and from the drum, the heat would dissipate onto the conveyor belt. In order to achieve any heat transfer from the drum motor to the belt, the drum motor could not be covered with rubber lagging. However, most of the drum motors sold today are lagged with rubber, making it extremely difficult, if not impossible, to remove heat from the drum motor.
Most drum motor failures, regardless of the manufacturer, are related to the inability to extract and dissipate heat generated by the electric motor and the gear reducer. In 2012, the VDG research team began investigating how the lack of heat transfer affects the reliability of the drum motor. The findings were not encouraging.
On a drum motor without lagging and full belt contact, the amount of heat dissipated to the belt was only 26% of the required heat dissipation. When the same drum motor was tested with lagging, there was no measurable heat dissipation. In simple terms, a drum motor with lagging has no cooling. The second test was with an all-stainless steel drum motor driving a modular Intralox belt. The results were the same: no measurable amount of heat dissipation was recorded. In that case, the operating temperature of the electric motor with no cooling will continue to rise until the motor burns out. The lifespan of a motor exposed to those conditions and running under full load is unlikely to last more than 10 hours. Elevated temperatures also affect the lubrication properties of the oil. When the oil is exposed to the high temperature generated by the motor and gear reducer, it reduces the oil viscosity. Test results indicated that when the electric motor reached 100°C, the oil viscosity dropped from 220 centistokes (cSt) to less than 10 centistokes. With 10 centistokes of oil viscosity, the oil is no longer an effective lubricant and could cause gear and bearing damage. Since the drum motor is a hermetically sealed unit, the internal pressure can climb to approximately 18 psi, which reduces the integrity of the oil seals, causes oil leaks, and increases the overall temperature of the drum motor.
In conclusion, to obtain some reliability when a drum motor is used to drive a belt conveyor, the conveyor load should not exceed more than 60% of the drum motor horsepower rating. Anything above that will cause drum motor failure due to heat buildup. These types of failures have contributed to the common opinion that the drum motor is not a reliable choice as a conveyor belt drive and used mainly in applications where space is restricted for a traditional motor and gearbox drive. After an extensive 5-year research and development study, VDG developed an all-new drum motor design. The new generation of VDG Drum Motors has a cooler-running motor that does not require external cooling.
What makes the new generation design VDG drum motor the most reliable belt drive?
Knowing that a cooling mechanism for a drum motor was not feasible, the VDG design team focused their efforts on designing a drum motor that does not require cooling. In the original drum motor design, the gear reducer generated just 15% of the overall drum motor temperature, while the electric motor generated the remaining 85%.
The calculated maximum operating temperature for acceptable oil viscosity and effective lubrication of the gears and bearings in the drum motor cannot exceed 75°C. To achieve this goal was a tall order, considering the operating temperature of a standard electric motor is 80°C (temperature rise) plus an ambient temperature of 25°C, which brings the overall operating temperature to 105°C. Having a cooling fan on the standard electric motor made it possible to keep the motor temperature at an acceptable operating level. A cooling fan is not possible with the drum motor design.
To design an electric motor that does not require external cooling, copper and iron losses had to be minimized and electrical and mechanical efficiencies increased. Calculating new electric motor windings with reduced magnetic and current densities for low-temperature emissions got VDG on the right track, but it wasn’t enough to reach the goal. The metallurgical composition of the stator core and rotor had to change with material containing less carbon and more iron to minimize the decrease in flux densities and reduce losses. High losses produce high temperatures, and low losses produce low temperatures.
In the new electric motor designs, the laminated stator core and rotor physical size had to be taken into consideration, as well as the length and diameter had to be increased to make up for the horsepower and torque lost by the reduction of the magnetic density. To reduce the operating temperature further, an equalization pressure valve had to be included in the design to prevent pressure build-up in the drum motor. This resulted in significantly increased oil seal service life, substantially better sealing, and reduced oil and motor temperatures.
Gear reducer assembly
The gear reducer had to be completely redesigned for increased efficiency and low dB noise levels, which are required in a number of industries, primarily the airline industry. Therefore, the VDG Drum Motor went through a total redesign program. All components of the new generation VDG Drum Motor are designed for 80,000 hours of continuous operation before maintenance. VDG achieved this by reducing the electric motor operating temperature and increasing the level of lubrication. However, the temperature reduction through minimization of losses only worked for motors up to and including 50 hp. Due to the thermodynamic changes that occur in a 75 hp and higher drum motor, an external oil cooler is required to maintain low motor and oil temperature. VDG has developed and patented a Cooling/Conditioning Unit that extracts the oil from the drum, filters it, cools it, and returns it to the drum motor. A 75 hp drum motor and higher, regardless of the manufacturer, will fail without an external oil cooler.
Conclusion
The VDG engineering team faced a huge challenge in developing and implementing the new motor design. Significant investments along with in-house design and manufacturing of all components, including electric motors and all gear reducers, made it possible for the engineering team at VDG to overcome heat issues experienced with all drum motors when it first entered the market. In mid-2021, VDG unveiled the new generation of VDG Drum Motor designs.
Note:
All of the above drum motor design improvements have been carried out by the VDG research and development team, and all new-generation drum motor components are manufactured by VDG exclusively for VDG Drum Motors. The designs are proprietary to VDG and do not apply to or cannot be followed by any other drum motor manufacturer.
Fresh ideas. Served daily. Subscribe to Dairy Processing's free newsletters to stay up to date about the latest dairy news. |
Subscribe |